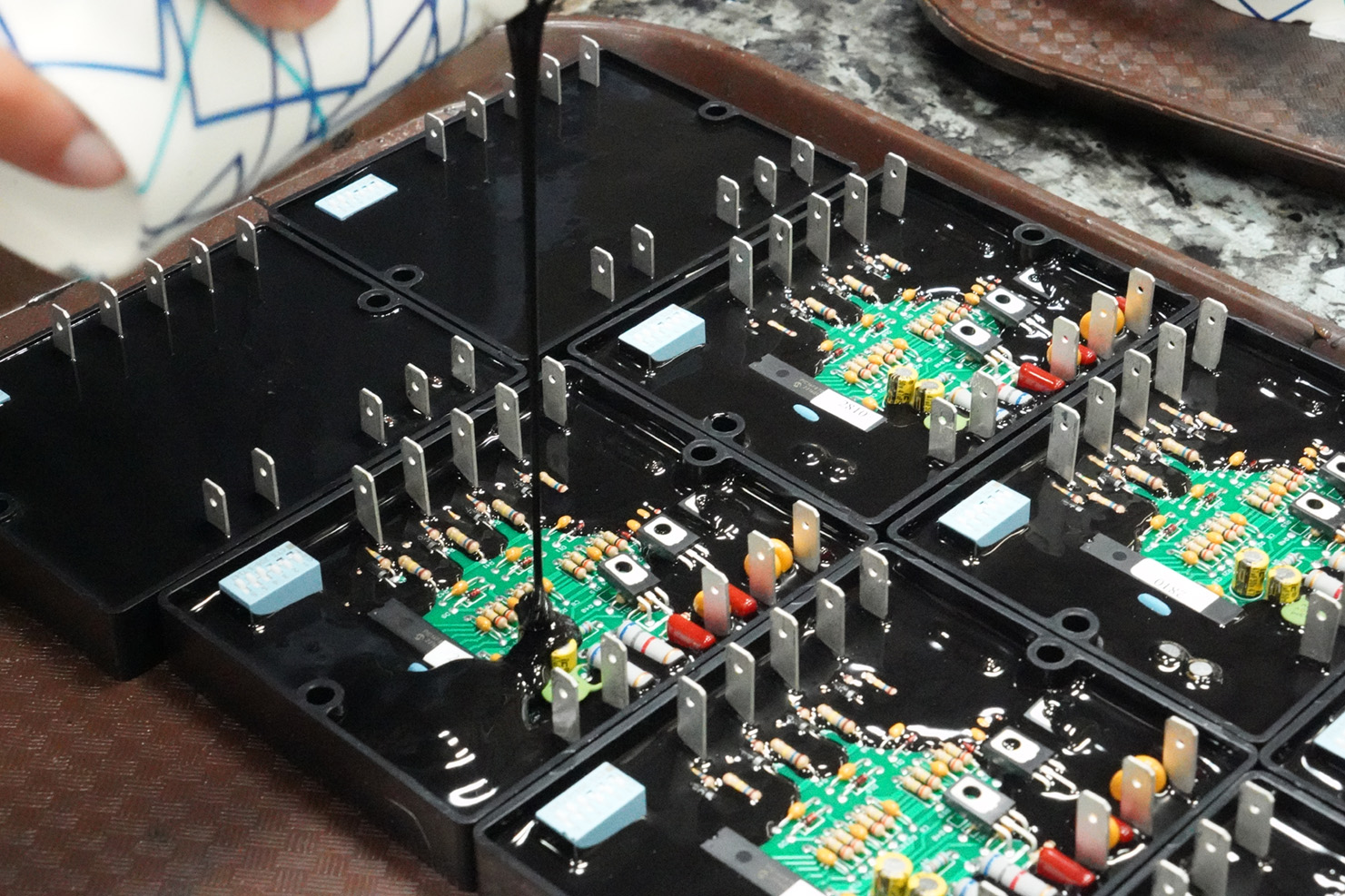
Epoxy Resin Encapsulation
What is PCB Potting or Encapsulation? Potting uses a “pot” or shell with a resin that fully envelopes the PCB electronics to protect against elements that may damage the function of the electronic components.
This is especially important when the electronic components are exposed to environmental hazards such as moisture spray, shock, vibration, and extreme thermal or corrosive chemicals.
Potting of strategic parts and components can significantly improve reliability and guard against premature aging and failure.
Precise Pour Hand Process
We pour, level, and fill the epoxy compound slowly and with precision to ensure all connection components, tabs, and plugs remain accessible but sealed. This provides a watertight encapsulation while minimizing bubbles and gaps.
Once completed, the pots cure for 24 hours or more in our environmentally controlled “cure room” to ensure the epoxy resin reaches its maximum strength.
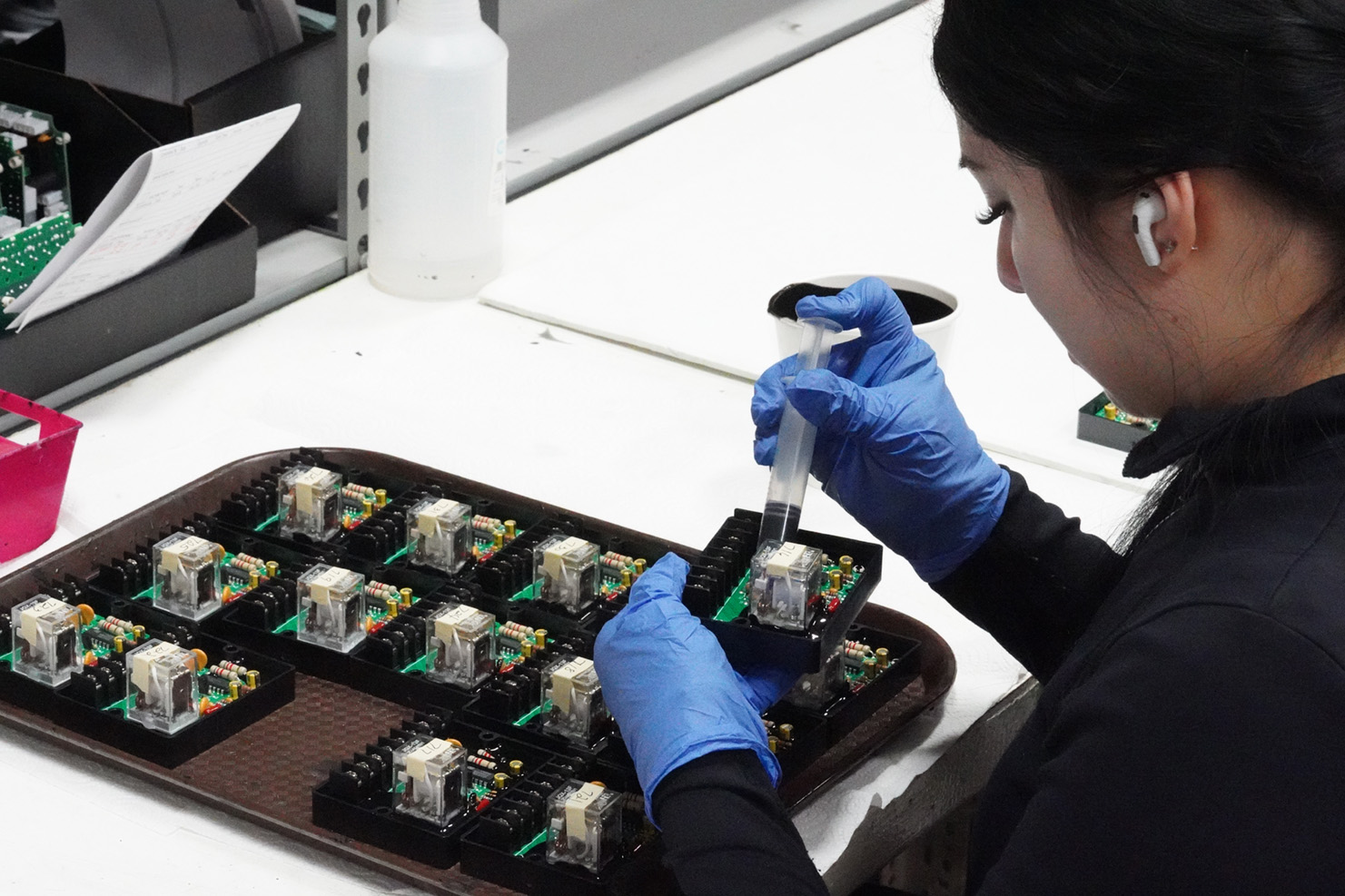
How to choose: Potting vs Conformal Coating
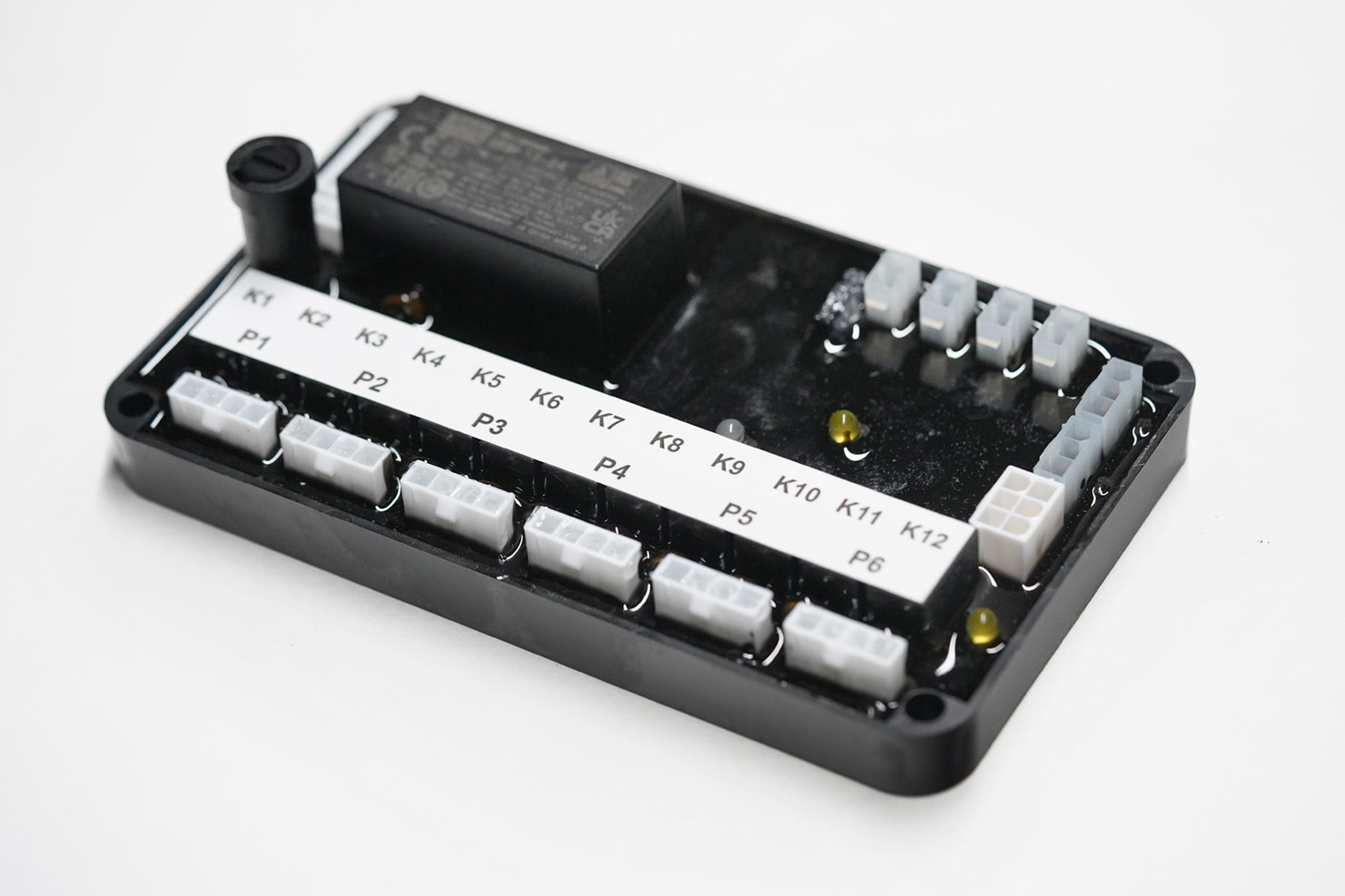
Potting Encapsulation
Typically used when environmental risks are inherent to the function of the PCB. Automotive, transit, commercial kitchen appliances, HVAC, home and garden, or agricultural systems that may all be exposed to dirt, liquids, moisture, vibration, and extreme temperatures are great examples.
Pros
+ Sealed electronic components provides maximum protection to environmental risks and moisture.
+ Allows for more mounting options for densely populated boards.
+ Increases lifespan of electronics by sealing from all exterior factors.
+ High level of protection to ensure functionality of mission critical components.
Cons
– Once sealed board cannot be reworked.
– Adds weight and bulk to the final product.
Weight could possibly stress some components.
– Curing times and process of pouring resin could lead to longer production times and cost.
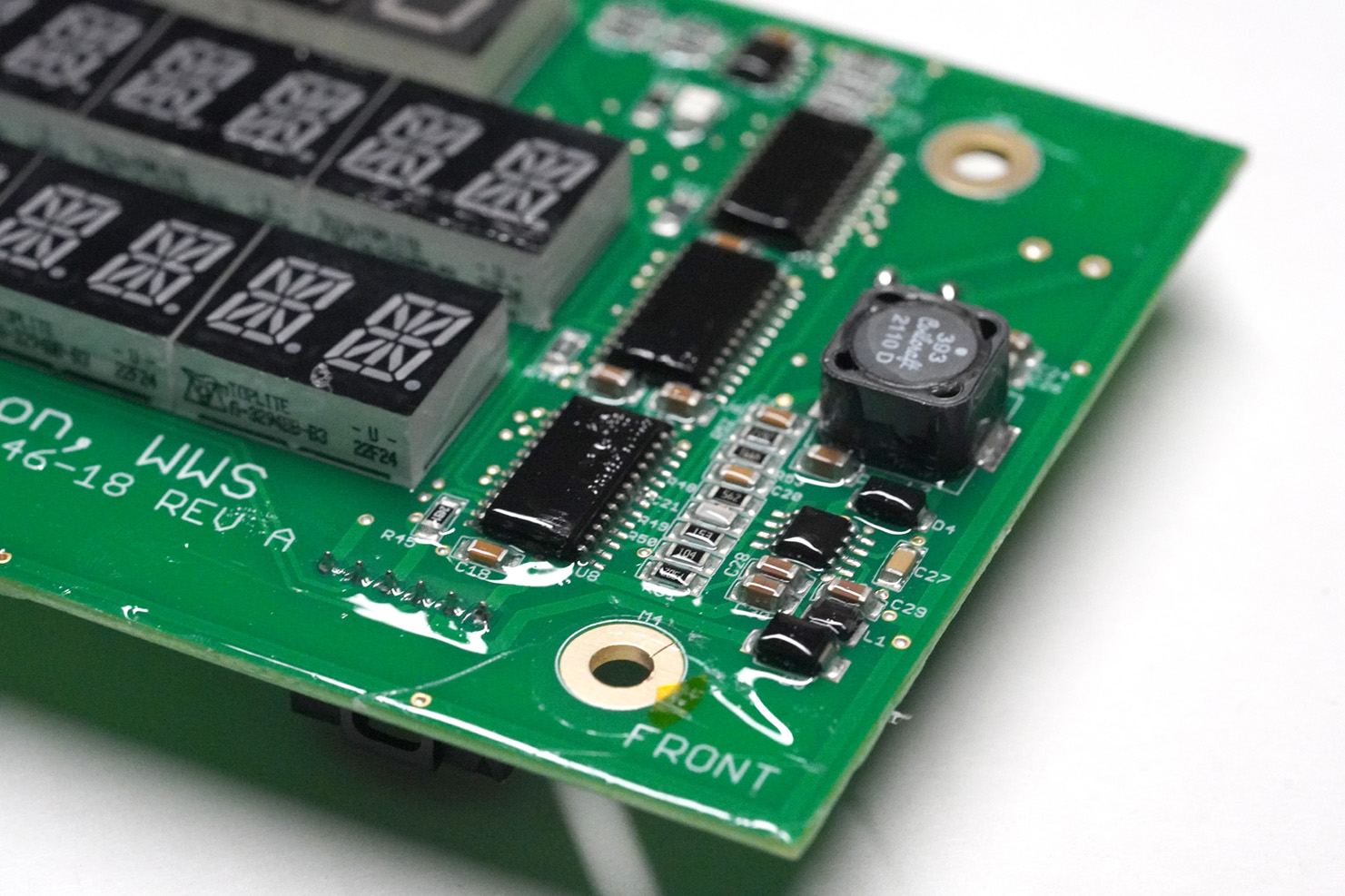
Conformal Coating
Typically used where environmental risks are possible but not always present that may harm mission-critical components over time. Conformal coating protects against humidity, thermal shock, static, vibration, and contamination.
Pros
+ Components remain visible and can be reworked or replaced if needed.
+ Thin and lightweight, offers flexibility with no stress on components.
+ Offers protection against low-level risks like dust, humidity, and corrosion.
+ Cost effective spray is faster for bulk production.
+ Long lasting protection over time
Cons
– Is not nearly as durable or resilient to heavy-duty environments.
– Is not waterproof or IPX6 rated.